Some time in the Viking Age, on the island of Gotland, a smith lost his large and heavy wooden toolchest in a bog. It may have been on a boat that capsized; it’s hard to be sure. Anyway, the chest—90 cm x 26 cm x 24 cm (almost three feet long, about ten inches wide and high)—and all its tools were preserved in the bog. The bog was drained between 1902 and 1910, and the chest was uncovered in 1936. It is now known as the Mästermyr chest and kept in the Swedish Historical Museum—which, all Gods be thanked, has a huge database of artifact images.
The chest included sledges and other hammers, and i
Some time in the Viking Age, on the island of Gotland, a smith lost his large and heavy wooden toolchest in a bog. It may have been on a boat that capsized; it’s hard to be sure. Anyway, the chest—90 cm x 26 cm x 24 cm (almost three feet long, about ten inches wide and high)—and all its tools were preserved in the bog. The bog was drained between 1902 and 1910, and the chest was uncovered in 1936. It is now known as the Mästermyr chest and kept in the Swedish Historical Museum—which, all Gods be thanked, has a huge database of artifact images.
The chest included sledges and other hammers, and it included what are said to be four anvils. (Here’s a link to the complete inventory; look for the word städ to see the anvils: Sökresultat föremål ) Obviously, these are not modern-style anvils; you couldn’t fit four of those into a box that size. Three of them look more or less like this one:
(Catalog no. 107115; image released CC-BY 2.5 SE)
That’s the striking surface to the right. The whole thing’s only about 7 cm long and 4 cm wide, so this is not a huge striking surface. The dull pointed end on the left was driven into a tree stump or something like that, for stability when in active use. There’s an Old English manuscript, MS Junius 11 in the Bodleian Library at Oxford, that shows the Biblical smith Tubalcain using what looks like this sort of anvil: a striking surface set into a larger block. (Link to the page: Search )
Two more artifacts from the Mästermyr chest are called sparrhorn in Swedish, which apparently translates to “bickern” in English—a word I had to go look up. A bickern is a horned or pronged anvil (the word comes from French bicorne), and one of the Mästermyr bickerns looks like this:
(Catalog no. 107118; image released CC-BY 2.5 SE)
I think the idea here is the same—you’d drive one end of this thing into a stump or some other steady surface that would hold it, and then you’d use the prong sticking out as an anvil horn if you needed one.
So in short: Viking-era smiths carried portable anvils that didn’t have a base, saving on both the weight and the quantity of iron required. Also, parts that are combined on a modern anvil, the horn and the striking surface, could be made separately. That doesn’t quite answer your question as such—but it does suggest how the cost of an anvil in Viking times was kept down to a manageable level.
PS: If the sizes of both the anvils depicted here seem small. . . the other finds in the Mästermyr chest included the remains of three padlocks. The owner seems to have specialized in relatively small objects—chain links, nails, locks and keys—and may not have needed a huge anvil, even if he could have afforded one. In fact, now that I think about it, I don’t think Viking-era smiths made really large constructions out of iron—no huge wrought iron gates or anything like that—and as a rule may have not needed especially large anvils at all. Anyone out there in Quoraland got more information?
All iron objects before the innovation of blast furnaces came from bloomeries. Raw iron ore was smelted in a chimney shaped furnace into a spongy bloom and then wrought (beaten) into a workable shape and alloy. The first iron anvils were simply very large blooms worked into a block with at least one flat surface. Iron in the quantities we are used to was unknown in the Middle Ages and if you have ever seen one being made you would know that making a large bloom that is of any quality is a very difficult task. Accordingly anvils were very expensive.
Since the question is about ancient times: in the stone age, stone knappers used large stones for anvils. After the discovery of metal, the first anvils were still stone: reconstructed Proto-Indo-European word for “stone” is *h₂ek'mōn, which in Greek language became the word for “anvil”, ákmōn. Only when metalworking advanced could the first metal anvils be made. A stone was, obviously, free, although perhaps there were usage rights?
Here is a photograph of a stone-age anvil:
Since the question is about ancient times: in the stone age, stone knappers used large stones for anvils. After the discovery of metal, the first anvils were still stone: reconstructed Proto-Indo-European word for “stone” is *h₂ek'mōn, which in Greek language became the word for “anvil”, ákmōn. Only when metalworking advanced could the first metal anvils be made. A stone was, obviously, free, although perhaps there were usage rights?
Here is a photograph of a stone-age anvil:
And another of a small portable stone-age anvil:
(Source: Anvil Stone, Carsethorn)
Up to the mid 19th century anvils were usually forged from forge welded lumps of wrought iron. They then received a working surface made up from a plate of steel (which could be hardened), which was forgewelded in place.
In the mid-19th century an American blacksmith developed an anvil cast from liquid steel. This has been the way of manufacturing anvils ever since. The working surface gets selectively hardened.
As for the shapes of the anvils, they varied depending on the use and the region. E.g. my anvil is a 50 kg one of the Belgian Liège type. The London pattern is very much used in the Engl
Up to the mid 19th century anvils were usually forged from forge welded lumps of wrought iron. They then received a working surface made up from a plate of steel (which could be hardened), which was forgewelded in place.
In the mid-19th century an American blacksmith developed an anvil cast from liquid steel. This has been the way of manufacturing anvils ever since. The working surface gets selectively hardened.
As for the shapes of the anvils, they varied depending on the use and the region. E.g. my anvil is a 50 kg one of the Belgian Liège type. The London pattern is very much used in the English speaking world. In Germany there are several regional patterns as well.
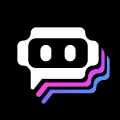
Anvils in medieval and ancient times were essential tools for blacksmiths and metalworkers. Their construction and cost varied by period and location, but here are the general methods of production and factors affecting their expense:
Construction of Anvils
- Materials:
- Anvils were primarily made from wrought iron or steel, which provided the necessary hardness and durability. Some early anvils were made from stone or cast iron, but these materials were less common. - Manufacturing Process:
- Forging: The most common method involved forging. Blacksmiths heated iron bars in a forge and then ha
Anvils in medieval and ancient times were essential tools for blacksmiths and metalworkers. Their construction and cost varied by period and location, but here are the general methods of production and factors affecting their expense:
Construction of Anvils
- Materials:
- Anvils were primarily made from wrought iron or steel, which provided the necessary hardness and durability. Some early anvils were made from stone or cast iron, but these materials were less common. - Manufacturing Process:
- Forging: The most common method involved forging. Blacksmiths heated iron bars in a forge and then hammered them into shape. This process could involve welding pieces together to form a solid block.
- Casting: In some cases, especially for larger anvils, casting was used. Molten iron was poured into a mold to create the anvil shape. This method allowed for greater consistency in size and shape.
- Finishing: After forming, anvils were ground and polished to create a smooth working surface. The face of the anvil was often hardened through quenching (rapid cooling) to improve wear resistance. - Design Features:
- Anvils typically featured a flat top surface (the "face"), a horn for shaping metal, and various holes (like the hardy hole and pritchel hole) for holding tools and shaping materials.
Cost of Anvils
The cost of anvils in medieval and ancient times depended on several factors:
- Material Quality: Higher quality materials and more sophisticated manufacturing techniques increased costs. Anvils made from high-carbon steel were more expensive than those made from wrought iron.
- Size and Weight: Larger and heavier anvils, which could withstand more significant impacts and provided a larger working surface, typically cost more.
- Regional Variations: The availability of materials and the local demand for blacksmithing tools influenced prices. Anvils could be relatively expensive in regions where they were scarce.
- Time Period: Over time, as blacksmithing techniques evolved and demand increased, prices could fluctuate.
Estimated Costs
- In medieval Europe, a basic anvil might have cost between 5 to 20 shillings, which was a significant investment for a blacksmith at the time. The price could be higher for larger or more finely crafted anvils.
- In ancient times, the costs could vary widely based on local economies. For example, in ancient Rome, the price of an anvil could range from a few denarii to several depending on its size and quality.
Conclusion
Overall, anvils were vital tools for metalworking, and their production involved skilled craftsmanship. Their cost reflected the materials used, the size, and the local economic conditions. While they were an essential investment for blacksmiths, the price was justified by their critical role in metalworking activities.
Where do I start?
I’m a huge financial nerd, and have spent an embarrassing amount of time talking to people about their money habits.
Here are the biggest mistakes people are making and how to fix them:
Not having a separate high interest savings account
Having a separate account allows you to see the results of all your hard work and keep your money separate so you're less tempted to spend it.
Plus with rates above 5.00%, the interest you can earn compared to most banks really adds up.
Here is a list of the top savings accounts available today. Deposit $5 before moving on because this is one of th
Where do I start?
I’m a huge financial nerd, and have spent an embarrassing amount of time talking to people about their money habits.
Here are the biggest mistakes people are making and how to fix them:
Not having a separate high interest savings account
Having a separate account allows you to see the results of all your hard work and keep your money separate so you're less tempted to spend it.
Plus with rates above 5.00%, the interest you can earn compared to most banks really adds up.
Here is a list of the top savings accounts available today. Deposit $5 before moving on because this is one of the biggest mistakes and easiest ones to fix.
Overpaying on car insurance
You’ve heard it a million times before, but the average American family still overspends by $417/year on car insurance.
If you’ve been with the same insurer for years, chances are you are one of them.
Pull up Coverage.com, a free site that will compare prices for you, answer the questions on the page, and it will show you how much you could be saving.
That’s it. You’ll likely be saving a bunch of money. Here’s a link to give it a try.
Consistently being in debt
If you’ve got $10K+ in debt (credit cards…medical bills…anything really) you could use a debt relief program and potentially reduce by over 20%.
Here’s how to see if you qualify:
Head over to this Debt Relief comparison website here, then simply answer the questions to see if you qualify.
It’s as simple as that. You’ll likely end up paying less than you owed before and you could be debt free in as little as 2 years.
Missing out on free money to invest
It’s no secret that millionaires love investing, but for the rest of us, it can seem out of reach.
Times have changed. There are a number of investing platforms that will give you a bonus to open an account and get started. All you have to do is open the account and invest at least $25, and you could get up to $1000 in bonus.
Pretty sweet deal right? Here is a link to some of the best options.
Having bad credit
A low credit score can come back to bite you in so many ways in the future.
From that next rental application to getting approved for any type of loan or credit card, if you have a bad history with credit, the good news is you can fix it.
Head over to BankRate.com and answer a few questions to see if you qualify. It only takes a few minutes and could save you from a major upset down the line.
How to get started
Hope this helps! Here are the links to get started:
Have a separate savings account
Stop overpaying for car insurance
Finally get out of debt
Start investing with a free bonus
Fix your credit
Further to Phillipa Alterton's answer, I recall an article on artisan gunmakers in what was once called the Afghan Tribal Region and before that, the North West Frontier.
A pair of beturbanned gunsmiths were shown beside their workbench, the stump of a tree that must have been a metre across, on it was a vintage LMG, possibly a Bren gun, that had been adapted by hand to fire soviet ammunition.
The tools were familiar but nothing that would have been out of place in a garden shed, except for a modest mechanic's vise and, I think, the sort of anvil described and depicted in Phillipa's article, a l
Further to Phillipa Alterton's answer, I recall an article on artisan gunmakers in what was once called the Afghan Tribal Region and before that, the North West Frontier.
A pair of beturbanned gunsmiths were shown beside their workbench, the stump of a tree that must have been a metre across, on it was a vintage LMG, possibly a Bren gun, that had been adapted by hand to fire soviet ammunition.
The tools were familiar but nothing that would have been out of place in a garden shed, except for a modest mechanic's vise and, I think, the sort of anvil described and depicted in Phillipa's article, a lump of metal set into the ‘rim' of the stump.
The stump was only about a foot tall, a half metre at most, and the pair obviously did most of their work sitting on carpets.
What most interested me at the time was a dished area that appeared to be identical to the depression in the middle of ‘shaping bowls' I had seen used to create reproduction plate armour.
I suspect that this photo represented a straight line between the early iron age and the modern era, only the nature of weapons having fundamentally altered, the hand tools used to create, adapt and repair them virtually unchanged.
If you think of how difficult it was to produce iron from ore, than you will know and understand how expensive it was. A medieval sword was valued one horse.
The only iron they had was wrought iron as they could not melt thus cast it.
So I don't think they had anvils the way and form we have, but none, as far as I know, is left.
Here’s the thing: I wish I had known these money secrets sooner. They’ve helped so many people save hundreds, secure their family’s future, and grow their bank accounts—myself included.
And honestly? Putting them to use was way easier than I expected. I bet you can knock out at least three or four of these right now—yes, even from your phone.
Don’t wait like I did. Go ahead and start using these money secrets today!
1. Cancel Your Car Insurance
You might not even realize it, but your car insurance company is probably overcharging you. In fact, they’re kind of counting on you not noticing. Luckily,
Here’s the thing: I wish I had known these money secrets sooner. They’ve helped so many people save hundreds, secure their family’s future, and grow their bank accounts—myself included.
And honestly? Putting them to use was way easier than I expected. I bet you can knock out at least three or four of these right now—yes, even from your phone.
Don’t wait like I did. Go ahead and start using these money secrets today!
1. Cancel Your Car Insurance
You might not even realize it, but your car insurance company is probably overcharging you. In fact, they’re kind of counting on you not noticing. Luckily, this problem is easy to fix.
Don’t waste your time browsing insurance sites for a better deal. A company called Insurify shows you all your options at once — people who do this save up to $996 per year.
If you tell them a bit about yourself and your vehicle, they’ll send you personalized quotes so you can compare them and find the best one for you.
Tired of overpaying for car insurance? It takes just five minutes to compare your options with Insurify and see how much you could save on car insurance.
2. Ask This Company to Get a Big Chunk of Your Debt Forgiven
A company called National Debt Relief could convince your lenders to simply get rid of a big chunk of what you owe. No bankruptcy, no loans — you don’t even need to have good credit.
If you owe at least $10,000 in unsecured debt (credit card debt, personal loans, medical bills, etc.), National Debt Relief’s experts will build you a monthly payment plan. As your payments add up, they negotiate with your creditors to reduce the amount you owe. You then pay off the rest in a lump sum.
On average, you could become debt-free within 24 to 48 months. It takes less than a minute to sign up and see how much debt you could get rid of.
3. You Can Become a Real Estate Investor for as Little as $10
Take a look at some of the world’s wealthiest people. What do they have in common? Many invest in large private real estate deals. And here’s the thing: There’s no reason you can’t, too — for as little as $10.
An investment called the Fundrise Flagship Fund lets you get started in the world of real estate by giving you access to a low-cost, diversified portfolio of private real estate. The best part? You don’t have to be the landlord. The Flagship Fund does all the heavy lifting.
With an initial investment as low as $10, your money will be invested in the Fund, which already owns more than $1 billion worth of real estate around the country, from apartment complexes to the thriving housing rental market to larger last-mile e-commerce logistics centers.
Want to invest more? Many investors choose to invest $1,000 or more. This is a Fund that can fit any type of investor’s needs. Once invested, you can track your performance from your phone and watch as properties are acquired, improved, and operated. As properties generate cash flow, you could earn money through quarterly dividend payments. And over time, you could earn money off the potential appreciation of the properties.
So if you want to get started in the world of real-estate investing, it takes just a few minutes to sign up and create an account with the Fundrise Flagship Fund.
This is a paid advertisement. Carefully consider the investment objectives, risks, charges and expenses of the Fundrise Real Estate Fund before investing. This and other information can be found in the Fund’s prospectus. Read them carefully before investing.
4. Earn Up to $50 this Month By Answering Survey Questions About the News — It’s Anonymous
The news is a heated subject these days. It’s hard not to have an opinion on it.
Good news: A website called YouGov will pay you up to $50 or more this month just to answer survey questions about politics, the economy, and other hot news topics.
Plus, it’s totally anonymous, so no one will judge you for that hot take.
When you take a quick survey (some are less than three minutes), you’ll earn points you can exchange for up to $50 in cash or gift cards to places like Walmart and Amazon. Plus, Penny Hoarder readers will get an extra 500 points for registering and another 1,000 points after completing their first survey.
It takes just a few minutes to sign up and take your first survey, and you’ll receive your points immediately.
5. This Online Bank Account Pays 10x More Interest Than Your Traditional Bank
If you bank at a traditional brick-and-mortar bank, your money probably isn’t growing much (c’mon, 0.40% is basically nothing).1
But there’s good news: With SoFi Checking and Savings (member FDIC), you stand to gain up to a hefty 3.80% APY on savings when you set up a direct deposit or have $5,000 or more in Qualifying Deposits and 0.50% APY on checking balances2 — savings APY is 10 times more than the national average.1
Right now, a direct deposit of at least $1K not only sets you up for higher returns but also brings you closer to earning up to a $300 welcome bonus (terms apply).3
You can easily deposit checks via your phone’s camera, transfer funds, and get customer service via chat or phone call. There are no account fees, no monthly fees and no overdraft fees.* And your money is FDIC insured (up to $3M of additional FDIC insurance through the SoFi Insured Deposit Program).4
It’s quick and easy to open an account with SoFi Checking and Savings (member FDIC) and watch your money grow faster than ever.
Read Disclaimer
5. Stop Paying Your Credit Card Company
If you have credit card debt, you know. The anxiety, the interest rates, the fear you’re never going to escape… but a website called AmONE wants to help.
If you owe your credit card companies $100,000 or less, AmONE will match you with a low-interest loan you can use to pay off every single one of your balances.
The benefit? You’ll be left with one bill to pay each month. And because personal loans have lower interest rates (AmONE rates start at 6.40% APR), you’ll get out of debt that much faster.
It takes less than a minute and just 10 questions to see what loans you qualify for.
6. Earn Up to $225 This Month Playing Games on Your Phone
Ever wish you could get paid just for messing around with your phone? Guess what? You totally can.
Swagbucks will pay you up to $225 a month just for installing and playing games on your phone. That’s it. Just download the app, pick the games you like, and get to playing. Don’t worry; they’ll give you plenty of games to choose from every day so you won’t get bored, and the more you play, the more you can earn.
This might sound too good to be true, but it’s already paid its users more than $429 million. You won’t get rich playing games on Swagbucks, but you could earn enough for a few grocery trips or pay a few bills every month. Not too shabby, right?
Ready to get paid while you play? Download and install the Swagbucks app today, and see how much you can earn!
My online search shows 20 shillings or 1 pound. A riding horse in the 13th century went for about 10 pounds. A carpenter made about 3 shillings a day. So an anvil would be about a week's wages for a skilled worker. Median for a carpenter in the US was $19.00/hr so $760.00. A 275lb anvil from Rigid online goes for about $2000.00. Of course anvils are not produced In huge quality so it is a specialty item.
Such tools are refinements of simpler items. The second hammer was a rock if we allow that the first was a fist.
Likewise, another rock was the second or third anvil, following after dirt for the first and a log or tree stump for the second. You'll find stumps in use today, in shops that form sheet metal: jewelers, armorers, tin and coppersmiths, and custom car body builders, aka coachbuilders.
Much the same, the first tongs were fingers. Some primordial Ogg, tired of smashing his or her digits, took a split twig or folded a green branch to hold their work.
Okay, I know you're well into “get to t
Such tools are refinements of simpler items. The second hammer was a rock if we allow that the first was a fist.
Likewise, another rock was the second or third anvil, following after dirt for the first and a log or tree stump for the second. You'll find stumps in use today, in shops that form sheet metal: jewelers, armorers, tin and coppersmiths, and custom car body builders, aka coachbuilders.
Much the same, the first tongs were fingers. Some primordial Ogg, tired of smashing his or her digits, took a split twig or folded a green branch to hold their work.
Okay, I know you're well into “get to the point, Halberstadt!” territory: “How did they make them in STEEL, DAMMIT!?
To understand this it helps to understand primitive foundry work post working exclusively in naturally occurring metals, iow, smelted ores.
Take a hunk of copper ore, like malachite or azurite. Drop it in your campfire. If the fire's hot enough and you're lucky, there will be little bits of copper found in the slag after the fire goes out.
Still with me?
The easy way to get the copper “prills” out of the slag is by crushing. And since we don't have a proper hammer or anvil yet, we get to use a rock and another rock. (By this time Ogg has learned how to attach a handle to her rock…) Hello, Hammer Prime.
Still hanging on? Nice. Thanks! We're getting close!
You could do good work today with only a few additional bits to produce more copper and less slag from a given volume of ore.
Iron isn't quite so easy. Take a bunch of black sand, dump it into a furnace full of hardwood charcoal, heat the sucker up as hot as you can… and what comes out is a bit of “bloom”: really, really, REALLY low grade iron with lots of impurities in it. Turning that into something that won't disintegrate when looked at askance needs some doing.
With a hammerstone. On a rock, because we still don't have anything else.
But it isn't copper! Poor Ogg - put in all those hours of smelting and hammering and all she got was a lump of “rock” that's not good for nothing, nohow, kind of like her boyfriend, Lrrr.
But it made a good anvil for processing copper slag, sort of, and had far too much invested in it to toss.
And it made a nice side project given leisure time, and if she took some that didn't get tossed last time and used that to hammer the current batch on? They stuck together if it was hot enough.
Note: yes, it's anthropologically unlikely that the first smiths were female, but given their penchant for practicality and intelligence, the time frame and area, I believe it's possible and maybe even likely.
How did the first blacksmith in history make their hammer, tongs, and anvil?
Medieval swords cost from a little to a lot.
An archer might spend a few days' wages on a cheap hanger sword.
A man at arms, a knight, or a noble might spend much more.
Might take the pay from a week to years of work or service for the very best. A king’s ransom for some.
Medieval swords cost from a little to a lot.
An archer might spend a few days' wages on a cheap hanger sword.
A man at arms, a knight, or a noble might spend much more.
Might take the pay from a week to years of work or service for the very best. A king’s ransom for some.
TL,DR: They probably used stones and sticks.
Others have commented that you can make tongs without having tongs. It’s true, and tongs were the very first blacksmith project I made once I set up a forge. I made them from a yard-long bar of mild steel that I found. I used those tongs for the next few projects, until I got tired of them and made a better pair. I don’t think I used the first pair to make the second pair, either.
However, I doubt that the first blacksmith in history made their tongs the way described, which involves taking a long enough bar of steel/iron and working one end while hol
TL,DR: They probably used stones and sticks.
Others have commented that you can make tongs without having tongs. It’s true, and tongs were the very first blacksmith project I made once I set up a forge. I made them from a yard-long bar of mild steel that I found. I used those tongs for the next few projects, until I got tired of them and made a better pair. I don’t think I used the first pair to make the second pair, either.
However, I doubt that the first blacksmith in history made their tongs the way described, which involves taking a long enough bar of steel/iron and working one end while holding the other. Early blacksmiths did not usually have long bars of steel available. They instead started with a bloom, a spongy mass of iron and slag as it comes from the bloomery (a reducing furnace operating a little below the melting temperature of the iron), that had to be worked with a hammer to form into a solid piece of wrought iron (with much less slag). Any bar stock they had was the result of hammering out the wrought iron into the shape they wanted, and probably welding several pieces together to make the longer bar. Archaeologists have found evidence of this working process in the iron implements they’ve discovered.
There are still some blacksmiths in the third world that use stone hammers and anvils, and they sometimes use a bent green stick or two sticks as their tongs. The stone hammers and anvils are often chosen so that they’re useful without additional shaping. The green wood works pretty well as tongs, and are much easier to come by in less developed areas, so the tongs are replaced when they char past usability. The stones are harder and cheaper than bronze, and work well, and the sticks are much cheaper than bronze, and also work well. I suspect that the earliest smiths would have used stones and sticks, even though bronze was likely available.
Many of these smiths work with a helper or two, so they’ve got four or six hands available—often, it’s two hands for the bellows, two hands on the striker, and two hands holding the work.
From Arm and a Leg, to almost nothing. I know this is a bit of a copout but this is a very broad question. So let’s start with a little explanation
Medieval Times are 1,000 years in length. During this time technology changed, which is one reason why at the beginning of this age you had metal works being very expensive, and most people wearing padded clothing for armor (Gambeson) , to what we now call a Full Plate Armor. Similarly with weapons.
During 5th Century Swords were not a weapon that majority of people could get, while at the end of the Medieval age (around 16th Century) pretty much any
From Arm and a Leg, to almost nothing. I know this is a bit of a copout but this is a very broad question. So let’s start with a little explanation
Medieval Times are 1,000 years in length. During this time technology changed, which is one reason why at the beginning of this age you had metal works being very expensive, and most people wearing padded clothing for armor (Gambeson) , to what we now call a Full Plate Armor. Similarly with weapons.
During 5th Century Swords were not a weapon that majority of people could get, while at the end of the Medieval age (around 16th Century) pretty much anybody could afford one.
How long does it make a sword? Even that varies. A cheap sword could take a day or two to make, while a master worked Pattern Welded sword could take a week or more to make. In addition to just the blade itself, a true work of art weapon would have expensive pommel made with a work of art scabbard which combine could take a month or even longer at times.
Consider these two examples of weapons:
These kinds of swords would take very long time to make, would take a real master, and would be well above a commoner means to purchase.
Yet look at this sword:
(these swords were actually of good quality or they wouldn’t have survived, but these were warrior swords and meant for war and not status symbols so that gives you an idea).
This is what you are dealing with.
To summarize, depended on which time period, which location, and the means of the buyer, the sword could range from being exceptionally expensive to cheap, second hand item that every soldier (or even every common in some instances) could buy.
Compare this to modern times. Think about cars of the early 20th Century, vs cars today. At the dawn of the 20th century cars were toys to the rich, while at the end of the 20th century pretty much everybody can afford a car. However the rich can still have his Ferrari, while poor will be driving an old beat up GM POS.
Same with swords. In, let’s say 8th century swords were restricted to those people of means who could afford it. Your common man had a spear, maybe an axe, and a dagger. While by the 16th century every two bit mercenary had a sword, as they made great side arms.
In some times and places swords were a status symbol, that only nobility could get. While in other times everybody had an access to one.
Steel is made from iron and carbon. Iron was originally obtained from meteorites before 1200 BC. After that date, iron was refined from iron ore or bog iron. The Romans used slaves and condemned criminals to mine iron ore. (If the crime was heinous. Then they went to lead and mercury mines.) The mines were drained by treadmills. The slaves were given daily quotas to fill, maybe a certain amount of baskets. If they failed. They got beaten or didn't get rations of barley. There's more information written by Vitruvius. The town of Toletum now Toledo, Spain was the source of European steel in the
Steel is made from iron and carbon. Iron was originally obtained from meteorites before 1200 BC. After that date, iron was refined from iron ore or bog iron. The Romans used slaves and condemned criminals to mine iron ore. (If the crime was heinous. Then they went to lead and mercury mines.) The mines were drained by treadmills. The slaves were given daily quotas to fill, maybe a certain amount of baskets. If they failed. They got beaten or didn't get rations of barley. There's more information written by Vitruvius. The town of Toletum now Toledo, Spain was the source of European steel in the Roman and Middle Ages. However the best steel was wootz steel. It was sold in Damascus. It was imported all the way from southern India and Sri Lanka.
Medieval mining technology was described in the book “De Re Metallica" by Georgius Agricola. Since slavery was no longer popular and gunpowder arrived in Europe in the 1300s. They let the gunpowder do the smashing. To hoist water and ore, Agricola described machines powered by human, animal and water resources. Crucible steel was only developed in Sheffield England in the 1700s.
water wheel powered pump
animal powered bellows
human powered chain pump
Swords were very hard to make.
In medieval Europe there was no crucible steel, except as imports from India. The main material was was wrought iron. Thus, available steel had a lot of impurities which had to be removed and/or spread out. That required a lot of work and a lot of energy because charcoal isn’t great compared to modern coke. And then there was forging and reforging different materials to accomplish conflicting requirements: hard edge but soft and elastic sword. All that without any control in modern sense, from chemical purity to temperature.
Thin, cut oriented blades from late Medi
Swords were very hard to make.
In medieval Europe there was no crucible steel, except as imports from India. The main material was was wrought iron. Thus, available steel had a lot of impurities which had to be removed and/or spread out. That required a lot of work and a lot of energy because charcoal isn’t great compared to modern coke. And then there was forging and reforging different materials to accomplish conflicting requirements: hard edge but soft and elastic sword. All that without any control in modern sense, from chemical purity to temperature.
Thin, cut oriented blades from late Medieval and Renaissance period flex like a spring, they weren’t nothing like iron cudgels.
Speaking about cudgel, medieval blades were produced from fairly simple cross sections and small tapper to multiple, varying cross sections, with significant taper, with smooth blend between different cross section types.
So, traditional forging from multiple peaces of steel with impurities is absolutely incomparable to using modern spring steel like 1080, milling the blade from single block using modern machines and performing heating blade to very precise temperature. Even with modern steel, forging hexagonal cross section is not an easy task and requires a lot of work.
Of course, writers of fantasy genre, movie and TV authors are free to make everything easy and simple because they are not limited to facts and historical accuracy, even when they claim it.
Because they used iron and basic steel. The hyper alloys we use today are much stronger for what they are designed for, but are brittle in comparison and break quite easily, we use them for swords because they hold a good edge. But stainless sucks for swords. Basic 1060 or even 1085 steel is all you need for a good sword. People back then also carried thier swords everywhere and took care of them, so they got honed and oiled almost every day. Modern swords are made of stainless because people are to lazy to take care of thier swords and they rust. We also can't carry them all day and really ha
Because they used iron and basic steel. The hyper alloys we use today are much stronger for what they are designed for, but are brittle in comparison and break quite easily, we use them for swords because they hold a good edge. But stainless sucks for swords. Basic 1060 or even 1085 steel is all you need for a good sword. People back then also carried thier swords everywhere and took care of them, so they got honed and oiled almost every day. Modern swords are made of stainless because people are to lazy to take care of thier swords and they rust. We also can't carry them all day and really have no use for them anymore other than HEMA.
Arrow making was a professional skill. A craftsman who made them was called a fletcher.
Arrowheads were forged by blacksmiths, sometimes specialized arrowsmiths, while fletchers were responsible for finding suitable wood for shafts, shaping it and fitting the arrowheads and fletching on it. They would also repair damaged arrows for reuse. Arrows were quite expensive, so they were meticulously collected and reused whenever possible.
A hunter would have purchased his arrows from a fletcher, often commissioning them in advance and specifying the types he needed.
There would have been a fletcher’s wo
Arrow making was a professional skill. A craftsman who made them was called a fletcher.
Arrowheads were forged by blacksmiths, sometimes specialized arrowsmiths, while fletchers were responsible for finding suitable wood for shafts, shaping it and fitting the arrowheads and fletching on it. They would also repair damaged arrows for reuse. Arrows were quite expensive, so they were meticulously collected and reused whenever possible.
A hunter would have purchased his arrows from a fletcher, often commissioning them in advance and specifying the types he needed.
There would have been a fletcher’s workshop in every castle. Royal armories often employed a number of fletchers exclusively to produce arrows for the king’s army, and they would accompany armies on campaign to provide their services.
Erik Halberstadt’s answer is no doubt the truth. But there’s a different answer that you should be aware of.
For those that love woodworking and you're trying hard to discover detailed plans to build your dream project, you should check this link. They share list of 16000 projects with step by step plans. Each of the 16,000 projects are detailed enough to leave nothing to guesswork yet simple enough for beginners. Each projects included step-by-step instructions, cutting and materials lists, detailed schematics, views from all angles,.. It's easy to follow even I'm a beginner in this are.
The fa
Erik Halberstadt’s answer is no doubt the truth. But there’s a different answer that you should be aware of.
For those that love woodworking and you're trying hard to discover detailed plans to build your dream project, you should check this link. They share list of 16000 projects with step by step plans. Each of the 16,000 projects are detailed enough to leave nothing to guesswork yet simple enough for beginners. Each projects included step-by-step instructions, cutting and materials lists, detailed schematics, views from all angles,.. It's easy to follow even I'm a beginner in this are.
The fact is, Jewish scholars worried about this same question a couple of millenia ago. They concluded that, since you need tongs to make tongs, the first set of tongs must have been made by God Himself! (Herself? Themself? Itself?)
You can find this stated explicitly in the Talmud, specifically in the section called Ethics of the Fathers, chapter 5, verse 6. It reads as follows:
Ten things were created at twilight of the sabbath eve. These are: the mouth of the earth; the mouth of the well; the mouth of the donkey; the rainbow; the manna; the staff; the shamir; the writing, the inscription and the tablets. Some say also the burial place of Moses and the ram of Abraham. And some say also the spirits of destruction, and the original tongs, for tongs are made with tongs.
These are the supernatural things that were created at a very very special time: The end of the sixth day, after Man was created, but before the beginning of the first sabbath. To explain a few: the “mouth of the donkey” is Balaam’s donkey, which had the power of speech (Numbers 22); the “staff” is the staff of Moses; the “writing, inscription, and tablets” refer to the ten commandments; the “mouth of the earth” is the hole that swallowed Korach (Numbers 16:32).
No word on hammer and anvil.
It's a complex question, and yet vague at the same time. The answer really depends upon where, and more importantly when, you are. Copper was known and used, albiet very rarely, as tool material as far back as the 5th millennium BC. Thats the late Neolithic. By 3000 BC the Bronze Age was in full swing, bronze being an alloy of copper and tin that was tougher then either metal alone. Bronze eventually gave way to iron, which held sway reletivly briefly before being eclipsed by steel.
Here's where it gets really interesting. Some places produced better steel then otheres, and in a few rare occasi
It's a complex question, and yet vague at the same time. The answer really depends upon where, and more importantly when, you are. Copper was known and used, albiet very rarely, as tool material as far back as the 5th millennium BC. Thats the late Neolithic. By 3000 BC the Bronze Age was in full swing, bronze being an alloy of copper and tin that was tougher then either metal alone. Bronze eventually gave way to iron, which held sway reletivly briefly before being eclipsed by steel.
Here's where it gets really interesting. Some places produced better steel then otheres, and in a few rare occasions, much better. India, for example, has been a producer of high-quality steel almost from the alloy's discovery.
The smiths of the Far East are often touted as master steelmakers, but in actuality, it was the techniques used to forge the blades that were so advanced there, not the metal itself. Pretty standard crucible steel, for the most part.
Persia and its environs were famed for Damascus or Watered steel, today called Pattern-Welded steel. In this process, harder and softer steels (and occasinaly iron and steel) are forgewelded together, a laborious process that yields a very high grade alloy with a beautiful, almost water-like pattrern. Damascus was highly prized in the medieval period, but was around long before then.
In medieval times, such trends continued. Germany and Italy emerged as the finest steelmakers in Europe, likely due to the excellent iron ore avalable there. Damascus was still being imported as fast as it could be made, and in a few places used to create truly exemplary blades. The famed Ulfbrecht swords of Norse lore are a fine example of legendary weaponsmithing, built with imported watered steel.
By the late medieval period, metallurgy was getting much better. Mostly this trend was being driven by the need to come up with tougher steels for making gunbarrels. At this point, the focus shifted away from melee weapons, and by the end of the Renissance, making better steel for swords was mostly abandoned. Firearms had gained primacy on the field of battle, and blades were relegated to mere sidarms, and ceremonial weaponry.
The modern day trend of fancy alloys came about from formulating metal for tougher and stronger tools. Some alloys of modern steel can barely be called steel at all. Many hobby smiths, and more then a few commercial concerns, pride themselves on producing blades and tools “the old-fashioned way”, using techniques and alloys that would not be out of place in a 10th century forge. These weapons stack up quite favorably when compared to similar tools made using modern methods, but it takes considerably longer to hand-forge crucible steel then it does to dropforge modern alloys.
It's a facinating subject, and I've barely scratched the surface here. I'd strongly encourage you to do your own research on the topic; it's a highly rewarding field of study.
A cottage whould have set you back 5 shillings, Artisan house 20 shillings. Merchant house 2-3 pounds, Armour 100 shillings, War horse 50 shillings, Two Knight horse 10 pounds, High grade passenger horse 10 pounds, Wagon horse 10-20 shillings, The best wines from Gascony 4 pence a gallon, The best wines from the Rhine region 8 pence a gallon, Inexpensive wine 3-4 pence a gallon, Best wine 8-10 pence a gallon, Yule(high) 1.5 pence a gallon, Yule (medium) 1pence a gallon, Yule (low) 0.75 pence a gallon, Finest ale 1-1.25p a gallon, Second class ale 0.75-1p a gallon, Somerset best ale 1.25p a gal
A cottage whould have set you back 5 shillings, Artisan house 20 shillings. Merchant house 2-3 pounds, Armour 100 shillings, War horse 50 shillings, Two Knight horse 10 pounds, High grade passenger horse 10 pounds, Wagon horse 10-20 shillings, The best wines from Gascony 4 pence a gallon, The best wines from the Rhine region 8 pence a gallon, Inexpensive wine 3-4 pence a gallon, Best wine 8-10 pence a gallon, Yule(high) 1.5 pence a gallon, Yule (medium) 1pence a gallon, Yule (low) 0.75 pence a gallon, Finest ale 1-1.25p a gallon, Second class ale 0.75-1p a gallon, Somerset best ale 1.25p a gallon, Beer 1p a quart, Dried fruit (raisins, dates etc) 1-4 pence a pound, Spices ( cinnamon, cloves, mace, pepper, sugar etc) 1–3 shillings per pound, Saffron 12-15 shillings per pound, Good quality cattle 10 shillings, Cattle 9 shillings, Bull 13 shillings, Sheep 1 shilling, Somerset castrated ram in London 1 shilling, Somerset pigs 2 shillings, London pig 3 shillings, Two chickens 1 pence, Goose 6p, 80lbs Cheese 3 shillings and 4 pence, salted herring 5-10p, Salted fish 6p, Somerset oats l quarter 1 shilling, London oats 1 quarter 2 shillings,
Folks had figured out how to make swords from other metals for a very long time. Bronze ruled weapon-making for a considerable period.
Then came iron. Smiths in various parts of the ancient world began to figure out how to smelt iron from the raw ores. Iron is considerably stronger than bronze, but it does tend to be brittle. It can be forged into shape by heating red-hot and hammering.
Eventually, it was learned that the admixture of carbon from the forging fires made the iron harder and more importantly, less brittle.
This was not an instant discovery by any means, but eventually further proces
Folks had figured out how to make swords from other metals for a very long time. Bronze ruled weapon-making for a considerable period.
Then came iron. Smiths in various parts of the ancient world began to figure out how to smelt iron from the raw ores. Iron is considerably stronger than bronze, but it does tend to be brittle. It can be forged into shape by heating red-hot and hammering.
Eventually, it was learned that the admixture of carbon from the forging fires made the iron harder and more importantly, less brittle.
This was not an instant discovery by any means, but eventually further processes like “quenching” the hot steel and “tempering” the result at lower heat resulting in superior weapons… Strong and flexible:
(Read down to the “History” section)
The process for producing weapons stayed pretty much unchanged for hundreds of years… Produce steel from iron, forge it into at first rough and then close to final shape, and finish the blade with hand tools….Files and grinders and polishers. A tedious process, but with a virtual army of smiths in the ancient world, producing all manner of metal goods, armies and individuals could be supplied.
To vastly oversimplify, swords were normally sidearms used by wealthy or elite units that were able to afford them. Spears and lances had superior range, and so a relatively shorter sword would only be practical if this weapon broke or got disarmed. Archers who didn’t want to be weighed down by too much gear might have a sword or long dagger for self defense, as seen with Samurais, Arabs, Mongols, and English longbowmen. Even in armies that were famous for their swords, like Celts and Romans, the spear was still heavily used.
The middle ages is from the fall of the Western Roman Empire (476) to the Discovery of America (1492).
That’s more than 1000 years!
During the very early days getting your hands on a sword was really hard, not every legionnare had a sword by that time either, though gladii (which weren’t in use by this time) were about as long as the long knives of barbarians which almost everybody had. Spathae being longer took considerably more effort and skill to make and in some cases materials as well. Don’t forget gladii were relatively massive swords.
Now as we progress into the Middle Ages things don’t re
The middle ages is from the fall of the Western Roman Empire (476) to the Discovery of America (1492).
That’s more than 1000 years!
During the very early days getting your hands on a sword was really hard, not every legionnare had a sword by that time either, though gladii (which weren’t in use by this time) were about as long as the long knives of barbarians which almost everybody had. Spathae being longer took considerably more effort and skill to make and in some cases materials as well. Don’t forget gladii were relatively massive swords.
Now as we progress into the Middle Ages things don’t really change up until the time of Charlemagne and in his time a sword could very well cost you a few heads worth of livestock. Then we start progressing into the Viking age, by the 11th century swords became a bit more common. Still expensive but there are now a lot more of them on the field.
And then in the 11th century water powered hammers and bellows appear and they spread like forest fires. This caused tens of thousands of watermills to appear throughout Europe as their purpose wasn’t only grinding grain anymore but could be used to operate machinery. This meant less labour, cheaper swords once again. Couple this with the advances of metallurgy which now could produce springy swords meant increased lifetime for swords as well and much more appearing on second hand markets which further drove the costs down.
In the 14th century the Black Death ravaged Europe and Asia and Africa, killing about 30–50% in all places where they were affected. And this meant that labour became expensive but there were an abundance of items left by those who perished which further drove the costs down and just after the plague a cost of a cheaper sword was so low, that the daily wage of any craftsman could get you one.
The cost of one sword didn’t get lower than that, at least I am not aware of it.
So in the early days a sword was really expensive but most still had acces to long hewing knives (much like machete). As we progress into the middle ages we see swords being more and more common and getting cheaper and by the late middle ages a sword could be as cheap as dirt, though it may have been a bit outdated as you were likely to get a second hand one. Which may have belonged to a noble at one point and would have cost you an arm and leg back then but hey fashion AND battlefield circumstances made it outdated. The popularity of swords show as by the late 14th century the sword became an everyday sidearm for nobility and a lot of commoners as well.
Now how long would it have taken you to make such a sword in said periods? In the early days pattern welding was a must and it made them considerably longer to make but by the end of the period heat treatment was a factor so… a sword purely for function would have taken you about a week, a decorative one could have been much longer. But one workshop can work on multiple projects at once. Let’s say the swordsmith’s shop makes 50 blades every week and sends them out for heat treatment at the end of the week, they do the heat treatment in 2 days for the 50 blades, then they send it to the cutlers to assemble it with the fittings, it takes another couple of days, then they send it to the polishers who sharpen the blades and it takes another couple of days. And at the end let’s say 3–4 weeks we’ve got 50 swords done from start to finish but the next week we will get another 50 and then another. You get it.
And just to give some weight to my point the Swedish king Karl Gustav in the 16th century ordered 300 000 swords from Solingen and he wanted it delivered to Sweden in 6 months and they did it.
Multiple people working together can produce things much more efficiently than one man doing everything and from the mining process to the last polish it is all teamwork. This made it feasible to make a large amount of weapons, armour and anything else really in big quantities in a short time without impacting the quality.
Casting, at first. Which is where you heat the metal to liquid and then pour it into a pre-shaped mould. Bronze and copper are a nightmare to forge, so it was cast and grind. After iron became the material of choice, the first smiths tried casting, then started forging. Which is when you get the metal hot, and beatbit into shape with a hammer.
Bows made in the period up to about 1945, were made in the same manner as medieval bows in Europe. Once fiberglass came into play things changed. Bows from Eastern and middle Eastern areas were more like modern bows, being made in many cases, out of laminates involving horn and other natural materials other than wood. There are many bowyers today, who still make bows in the old manner, often referred to as “Primitive Archery”. Modern Compound bows have as much in common with modern crossbows as traditional bows. Traditional bows are made from seasoned wood, shaped and bent to a desired profile
Bows made in the period up to about 1945, were made in the same manner as medieval bows in Europe. Once fiberglass came into play things changed. Bows from Eastern and middle Eastern areas were more like modern bows, being made in many cases, out of laminates involving horn and other natural materials other than wood. There are many bowyers today, who still make bows in the old manner, often referred to as “Primitive Archery”. Modern Compound bows have as much in common with modern crossbows as traditional bows. Traditional bows are made from seasoned wood, shaped and bent to a desired profile, usually with hand tools. Some have a backing of sinew or snakeskin, or varying woods selected to provide the characteristics desired. While synthetic strings predominate, many traditional bows have flax or silk strings.
Swords in Medieval times were not cheap or easy to build. Most quality swords were made for Land owners and Royals. During a trip to Germany many years ago I saw Swords that were 600 years old that would cut a person in two. Never underestimate a sword in the hands of a Master Swordsman.
Swords may have been “relatively easy to make” but swords that didn’t bend, break or chip took a bit more knowledge, skill and time.
Whether due to technological advances or economic welfare we see that from the High Middle Ages onward people in Medieval Europe could consistently produce swords made entirely from steel (from multiple pieces welded together or a single piece). People also continued to produce swords where steel edges or tips were welded onto an iron body as done in earlier times.
Generally speaking, it was of much lower quality steel (and in earlier times, wer made of bronze). This is not to say that ALL ancient swords were of low quality steel, as there were a very few made of meteorite steel (Tutankhamen had one of these). Medieval steel was generally of higher quality due to the understanding that higher levels of carbon would create harder steel, and this was combined with things like welded pattern steel to create swords that not only could hold an extremely sharp edge, but were both strong and flexible as well. As well, some viking/early medieval swords were made
Generally speaking, it was of much lower quality steel (and in earlier times, wer made of bronze). This is not to say that ALL ancient swords were of low quality steel, as there were a very few made of meteorite steel (Tutankhamen had one of these). Medieval steel was generally of higher quality due to the understanding that higher levels of carbon would create harder steel, and this was combined with things like welded pattern steel to create swords that not only could hold an extremely sharp edge, but were both strong and flexible as well. As well, some viking/early medieval swords were made of a kind of steel imported from Persia and Northern India (Wootz) that was equal in most respects to the best of modern steels (such swords had the name ‘ULFBERHT’ on the blade in raised letters.
A Step Closer to the Mysterious Origin of the Viking Sword Ulfberht
It depends. Some only cost a few days labor, eg couple hundred bucks by todays equivalent. Others were worth more than your house. Depended on quality, style, place of origin, and time period.
They were typically made of various quality steel, depending on the weapons Smith who made them. The quality of any particular sword would be determined by how hot that Smith could get his forge. The hotter he could get it, the more carbon he could fold into the steel. Wood and coal only burn so hot. To get much higher temperatures, the Smiths of the best weapons would use coke which is made from coal and burns a great deal hotter.
After forging, the Smith would reheat and quench the blade, making it even stronger. This process is called annealing.
An anvil is just a big piece of cast metal. We’ve had the technology for casting for thousands of years.
Okay so first, medieval times encompasses a rather long span of time and cultures. Some cultures were still using bronze as late as the 1400s c.e. But let's focus on Europe from say, 1200 to 1400 c.e. the most common metal was iron.
For the most part, blacksmithing is a fairly cheap hobby. It’s possible to get a piece of stock, a hammer, and a forge-setup for less than 100$. The only real sore spot is the anvil, with many anvils selling at $3/lb or more.
- Few Companies Make Anvils
- Manufacturing and Design Concerns When Casting Steel
- Shipping & Handling Anvils Is A PITA
“Medieval" is quite broad term and whole process would be different in time and place but im case of brevity:
- They were hand hammered on the anvil. Lately maybe with help of water powered hammer.
- Quality varied — the top notch will be some Ulfberht and later damascuss blades due to steel quality.
- Compared to modern steel? Well, after 600 years of metalurgy development we can create far better, cleaner steels. No question there.
Steel is not easy to make. You need good quality iron, lots of heat lots of carbon, but not too much.
It was often easier to import it from thousands of miles away where smiths could create the blanks and you could then reforge and work it.
Smelting is a science, but for a long time was a dark art.
For a talented blacksmith? A pretty basic war sword could probably be made over a weekend, maybe a bit longer by the time everything is done. For something like an ornate sword for a lord or king would probably take a few weeks depending on the level of detail they would want.
For the most part, they were iron vs. steel. The standard sword was made from several different rods of iron, the outer edges being more malleable, while the center rod(s) were more brittle- this allowed the sword to be rigid enough, but not prone to breaking off (and easier to sharpen).
Large, hard already flat or flattened with a chisel stones on which soft metals can be shaped and struck between a hard hammer and a harder rock.
I know not the secrets of metal anvil making, such solid pieces of metal I do not know. But they did it some way somehow using our intelligence. Pretty amazing how people discovered things like copper smelting and casting alone but iron requires a much hotter flame rather amazing.